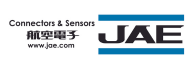

導入事例
製品のロスコスト194万円を削減した帳票電子化事例
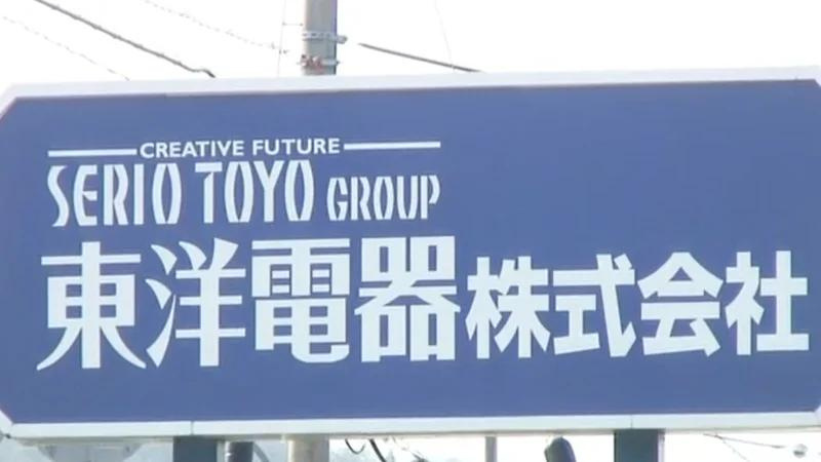
- 会社名
- 東洋電器株式会社(現:セリオ株式会社)
- 設立
- 1988年7月(昭和63年)
- 所在地
- 岡山県岡山市中区原尾島3-16-4
- 従業員数
- 290名 ※2023年4月現在
- 事業内容
- 製造業向けソフトウェアの開発
自動車の電子システム開発
モノリス型システムのクラウドネイティブ化
- ホームページ
- https://www.serio.inc/
良否判定や図解の表示で作業効率の向上を実現。知識や経験が共有に成功
『XC-Gate導入事例』東洋電器株式会社(現:セリオデベロップメント株式会社)
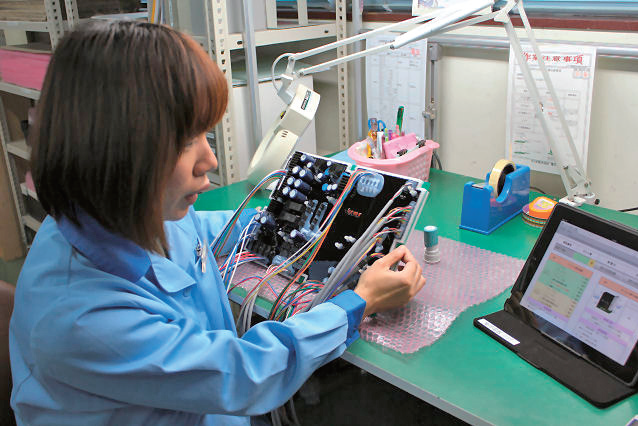
東洋電器(現:セリオデベロップメント)は、1972 年( 昭和47 年) に創業し、松下電器産業(現:パナソニック) が岡山県備前市に工場進出した際、協力工場としてVTR 製品や照明器具などの製造を開始した。同社はセリオ東洋グループ6 社の中で製造部門を担う会社である。
セリオ東洋グループは、岡山県に統括本社を置き兵庫県に工場、大阪府や京都府・愛知県・東京都に支店を持ち、ソフトウェアの設計から開発・製造に至るまでの「ものづくりIT サービス会社」である。
同社の代表的な製品は、電子制御応用機器、高速道路のLED 表示板ユニットや表示パネルだ。
XC-Gate導入事例
iPad を導入したのは、同社の基板製造グループで、設計から生産までを行い、医療・リハビリ機器の制御ユニットや農作物収穫機のコントローラなど、360 ほどの基板製品を取り扱っている。
従来、作業現場にはいくつかの課題があったという。基板製品は多品種少量生産で多くの種類があり、それぞれさまざまな工程手順があるにもかかわらず、1様式の工程管理表しか存在しなかった。製品によっては不要な工程も記されており、さらに手書きの修正なども重ねられているため、どの工程が必要で重要なのかを見極める熟練を必要としていた。
さらにプリント制御基板の製作現場では、作業内容は同じでも、作業担当者によって仕事のやり方が不規則で効率が悪く、今まで培われてきた知識や経験が共有化されていなかった。
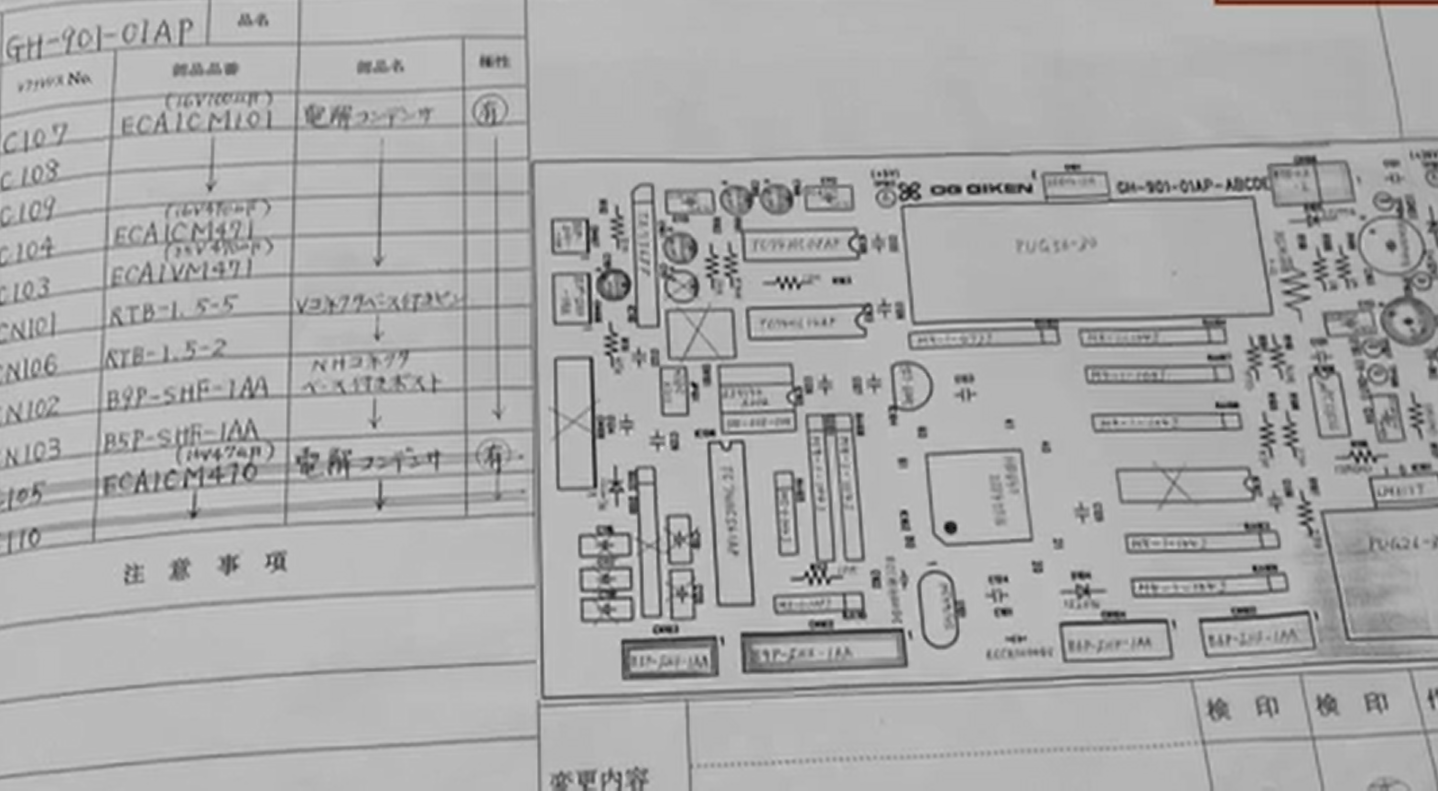
表示パネルに表す数字の角度やわずかな大きさの違いなども良否判定基準が定まっていないため、経験年数の浅い社員は判断することが難しい。
そこで、現場のメンバーがその都度仕事を一時中断し集まって相談していたが、20 分前後かかるため、作業効率が低下することがあった。これらのことを早急に改善することが当面の課題であったという。
そして、iPad 導入の背景を、東洋電器のシステム営業部 部長 野坂俊郎氏は次のように説明する。
「不適合品が散発的に発生していたため、2011 年4 月から2 カ月間、作業現場において基板製品の不良品調査を行いました。不適合品が1 件でも発生すると大切なお客さまにご迷惑をおかけします。
さらに、当社においても損失が発生しますから、発生件数を調べて、どうすれば品質向上につなげることができるかを確認することが重要でした。調査を行った結果、残念ながら2 カ月間で不適合品が10 件発生していました。10 件という数は非常に精度が悪く、抜本的に作業工程の見直しを図る必要がありました」
テクノツリーの帳票電子化システム「XC-Gate」を採用
東洋電器がiPad に着目するきっかけは、2011 年5 月に、東京で開催された「スマートフォン&モバイルEXPO 展」に、グループ代表取締役社長 壹岐敬氏がテクノツリー社のブースを訪れ、XC-Gate の優れた性能に着目したのがきっかけだった。
同社は作業効率を向上させるための手法として、作業工程管理システムであるXC-Gate を活用するため、工程管理表の異常警鐘機能や部品の良否判定ができる機能をテクノツリーの担当者と進めた。テクノツリーは、製造現場のシステム開発などで豊富な実績を持ち、タブレット型端末を活用したソリューションを提供している。iPad を利用した作業工程管理システムであるXC-Gate は、いつでもどこでも簡単に文書や点検表を閲覧し入力できる仕様になっている。会社の管理者はExcel ファイルで製品単位の工程管理表や出荷検査表の入力画面を作成し、XC-Gate サーバへデータを格納する。
そのデータを現場の作業工程担当者がiPad に取り込み、作業中に入力し送信することで、サーバ上にデータがアップロードされる。
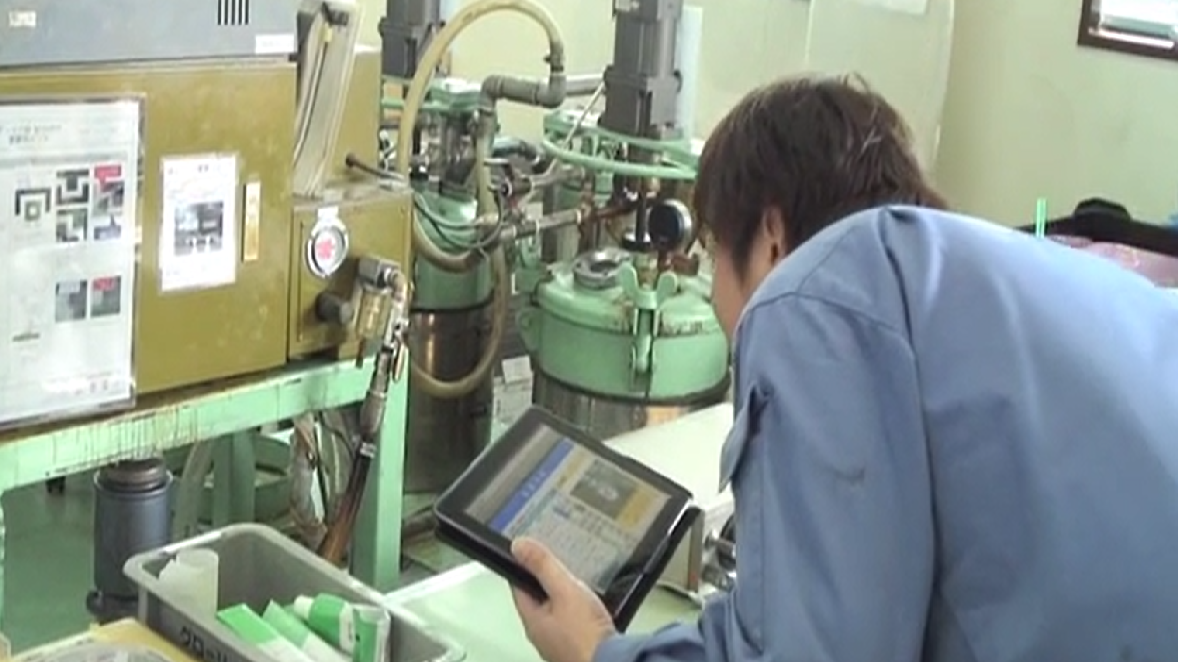
管理者は蓄積したデータをもとに、進捗確認やデータ分析を行っている。
同社の電子工場 製造部 課長の石原竜氏は、
「iPad とXC-Gateの組み合わせで工程管理システムを構築する際は、作業工程管理以外に受発注や勤怠などもしたいと思っていました。しかし、短期間にすべてを実装することは難しく、当社の問題としている生産性と品質向上を目的として、それを早急に改善したくテクノツリーの担当者と交渉し、提案からおよそ4 カ月で対応してもらいました。このシステムは2011 年9 月に完成し、同年10 月から運用開始しました。運用開始と同時に、工場内の現場スタッフへiPad を20 台配備しました」と語る。
良否判定や図解の表示で作業効率向上
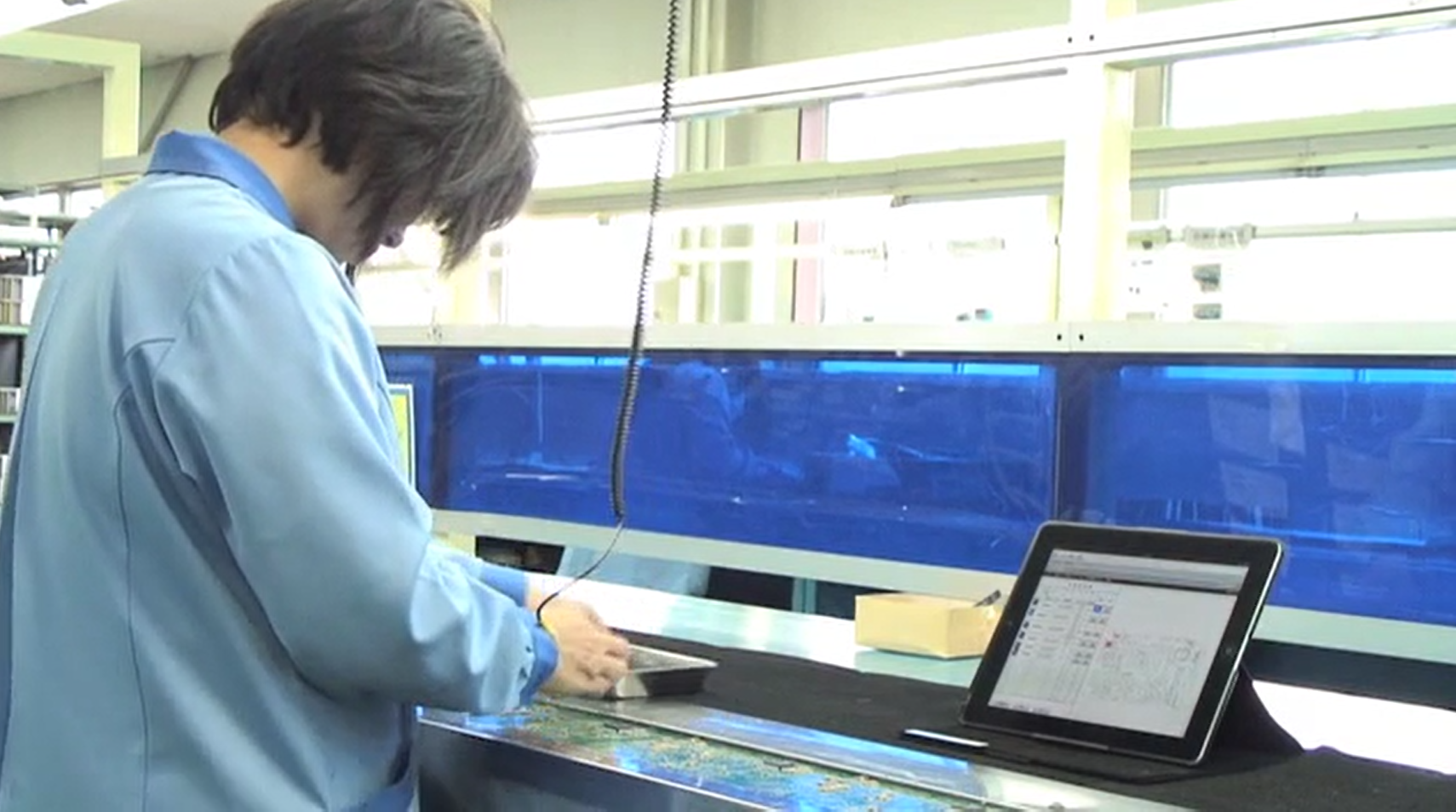
iPad には、およそ360 の基板製品の中から、毎月工場で製造される90 製品ほどの工程手順を優先して集約した。
製造頻度が高い製品の指示文書がiPad 上に明確に表示されるため、作業者は基準と照らし合わせて作業を行うことができる。図面上に良否判定基準を確認するための図解が表示されるため、良否の自己判断が可能になった。
また基板製品には、150 を超える細かな部品を挿入するものが多く、挿入箇所を探すのに時間がかかっていたという。そのためiPad 画面上の部品挿入図には、挿入箇所が色付け表示されるような仕様にした。さらに、従来の出荷検査表は文字の記載だけで分かりづらかったが、検査項目の図解も表示されるようになったため、作業担当者の理解が深まった。
工場の現場でiPad を利用する社員は次のように語る。
「従来は、紙の工程表や検査表をペンで1 件1 件項目ごとにチェックしていました。現在はiPad の画面に表示されている選択ボタンを押すだけで対応可能になりました。
従来、工程管理表は月に2000 枚を超える文書やチェックシートがあり、工程管理をそれぞれ確認するには時間的な無理がありました。
導入後は工程管理表や出荷検査表、部品挿入図、部品良否判定見本図などがiPad へ集約されているため、紙でチェックする必要もなく、部品の挿入間違いもなくなりました。また、紙の管理表や検査表を事前に印刷し準備する必要もなくなりました。作業処理時間は30 分前後早くなり、ペーパーレスにもつながっています。iPad は持ち運びが可能であり、図解が表示されるため見やすく基板製品の作業をしていくうえで、手放せなくなりました」
2011 年10 月にiPad を導入してから現場の作業工程は大きく変わってきた。さらに導入効果も見えはじめている。
同社の試算では、不適合品の発生抑制や作業工程上の無駄な時間の削減、ペーパーレスなどで年間およそ194 万円の削減が見込めるという。
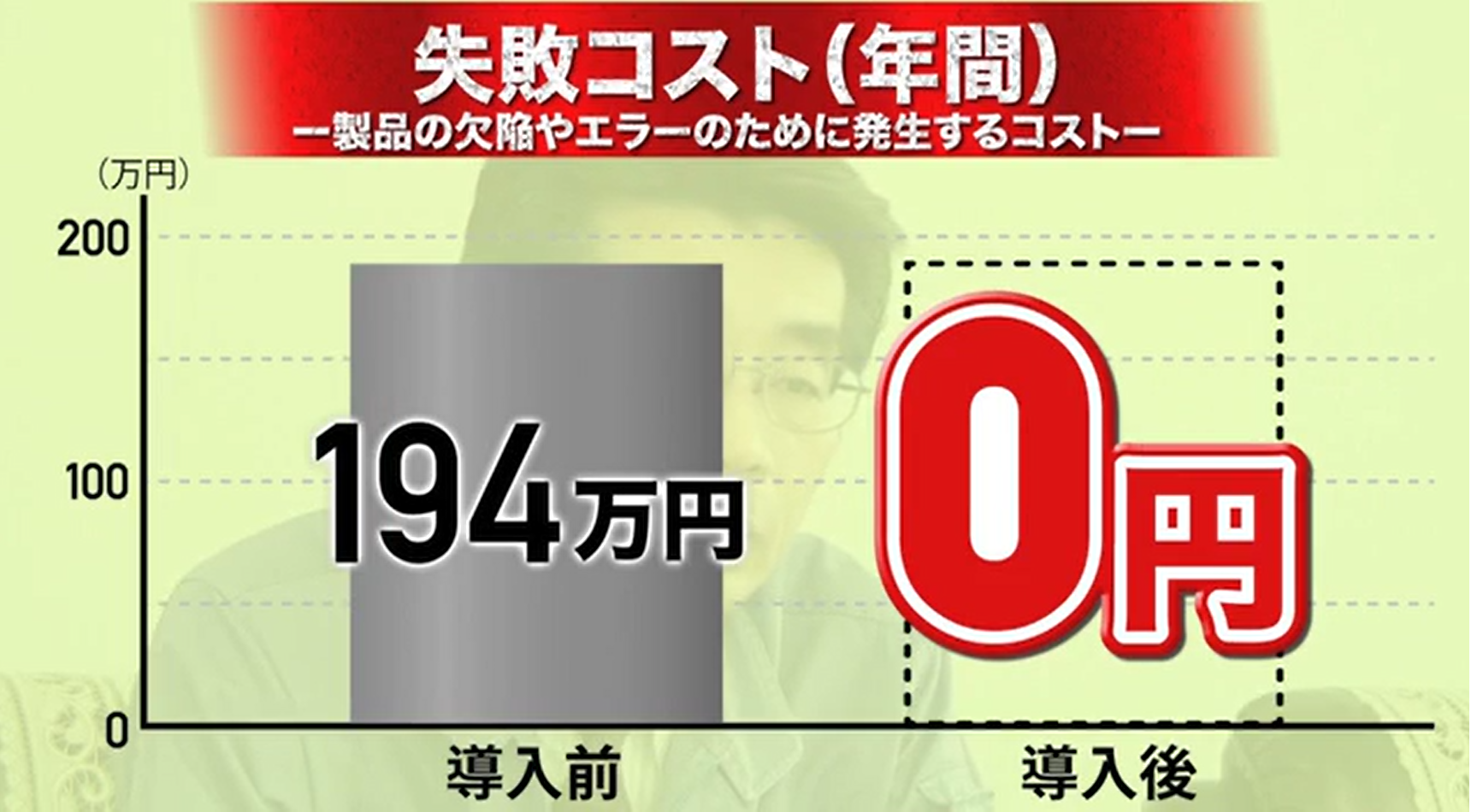
「iPad とXC-Gate を取り入れたことは、社員を成長させる良いきっかけになったと思います。工場内の社員は品質に対する意識が大きく変わり、作業工程上の不明瞭な点をはっきりさせるようになりました。それにより不適合品が減り品質が大きく向上したのです。品質と生産性を向上させることは、お客さまからの信用・信頼を得ることにつながります。作業工程管理システムを導入し、工場内の生産性は改善できました。今後は、作業工程において適正な時間配分をもって工程管理と生産管理を整えていきたいと思っています」(野坂氏)
東洋電器(現:セリオデベロップメント)様、
ご多忙の中、貴重なお話をお聞かせいただきありがとうございました。
製品に関するご質問がございましたら、お気軽にお問い合わせください。